Основы дизайна. Художественная обработка металла. Учебное пособие - Михаил Ермаков
Шрифт:
Интервал:
Закладка:
Молотки-наводильники служат для посадки гофр (рис. 3.8, а), гладильники – для правки и проковки поверхностей заготовки, шаровые – для выколотки вогнутых и выпуклых форм (3.8, в). Их бойки должны быть тщательно отполированы, чтобы не оставалось засечек и царапин.
Опорный инструмент представляют наковальни, плиты различных форм для правки и гибки листового металла, шпераки с двумя плечами различной формы – плоскими, конусными, округлыми концами (подробнее с приспособлениями можно ознакомиться в литературе по «Художественной ковке»). К опорному инструменту относятся стойны (рис. 3.8, б), служащие для обработки сложных по форме изделий. Массивные стойны с выпуклой поверхностью для выколотки и проковки полых изделий – амбусы. Используют слесарные инструменты – зубила, ручные ножницы, напильники, шаберы, плоскогубцы, круглогубцы, гофрилки, мерительный инструмент, чертилки, ножовки и др. свободной выколоткой выполняют в металле первые авторские образцы. Этот процесс трудоемкий и длительный, поэтому, если есть возможность, его заменяют другими, более производительными приемами – дифовкой по модели, давкой на станке.
Расплющивание производят молотком на небольшом участке листа, лежащего на наковальне. Толщина металла в этом месте уменьшается, раздается в ширь, и лист начинает деформироваться в сферическую поверхность, так как нетронутые его края не дают возможности раздаться в стороны.
Рис. 3.8. Основные инструменты: а – выколоточные фигурные молотки-наводильники; б – вертикальные стойна; в – гладильники.
Сгибание выполняют стальным или деревянным молотком на ребре наковальни. Оно может быть под углом, по прямой, дуге или радиусу. В качестве опоры выбирается ребро фасонной наковальни соответствующей формы. При сгибании происходит также и вытяжка металла. Осадка предполагает предварительную гофрировку заготовки, а затем осаживание гофры стальным или деревянным молотком на наковальне. Низкие и широкие гофры осаживаются легче. Губки плоскогубцев и круглогубцев для гофрировки или специальных гофрилок должны быть отполированы и закалены. Такой инструмент не оставляет царапин и повреждений на поверхности заготовки.
Материалом для ручной выколотки могут служить листы стали, алюминия, меди и ее сплавов, бронзы, латуни, томпаков; серебра и даже золота. Основное требование к материалу – пластичность. Единственное ограничение – толщина листового металла не должна превышать 2 мм. Бытовую посуду чаще всего изготовляют из обычной (лучше низкоуглеродистой) или нержавеющей стали, из алюминия, меди, латуни. При этом для улучшения потребительских свойств и увеличения срока службы стальную посуду принято лудить или эмалировать, медную – лудить, алюминиевую – оксидировать или покрывать слоем другого металла электролитическим способом.
Ручную выколотку выполняют на опорном инструменте – вертикальных стойнах – выколоточными фигурными молотками. Перед началом выколотки производят раскрой заготовок в соответствии с желаемой формой изделия. При раскрое необходимо учитывать припуски на осадку заготовки под ударами. Если выпуклость изделия будет высокой, припуск дают больше. Величину припусков для того или иного изделия лучше определять опытным путем. По мере накопления опыта вы научитесь безошибочно необходимые припуски. Очень важно перед началом работы внимательно осмотреть заготовку. Наличие на ней глубоких царапин, выбоин, других дефектов повышает риск разрыва заготовки под воздействием ударов на местах обнаруженных дефектов. Если дефектов поверхности заготовки не обнаружено, то ее в обязательном порядке отжигают для придания пластичности и лишь после этого приступают к выколотке.
В зависимости от конфигурации выбирают соответствующее стойно и расположив на нем плоскую заготовку, начинают выколачивать ее в необходимом месте, где планируется выпуклость. Выколотку ведут частыми, но не сильными ударами выколоточного молотка. Постепенно края заготовки отгибаются внутрь. На этом этапе выколачивают выпуклость высотой, равной 1/6-1/8 итоговой высоты выпуклости. Здесь делают остановку. Дело в том, что одновременно с подгибанием краев заготовки внутрь, на них образуются складки, называемые гофрами. Чем глубже выпуклость, тем сильнее гофрятся края заготовки. Изделие в готовом виде не должно иметь никаких гофров (конечно, если их наличие не задумано мастером). Поэтому процесс выколотки периодически прерывают и занимаются устранением гофров. Для этого их сначала выделяют с помощью круглогубцев, а затем осаживают молотком на стойне (рис. 3.9).
Устранив образовавшиеся на первом этапе гофры, переходят к выколотке середины заготовки. Середину выколачивают такими же частыми, равномерными, но не сильными ударами. Периодически удары прекращают, чтобы осмотреть изделие, не достаточна ли высота выпуклости, не произошло заваливания выпуклости и ее кромок в какую-либо сторону. Этот момент очень важен, так как несимметрично выколоченным изделием мастеру предстоит проводить трудоемкую, серьезную исправительную работу.
Маленький недочет всегда можно легко исправить несколькими ударами. При выколотке середины удары наносят от центра заготовки к краям по траектории расходящейся спирали. Но при этом удары по самой высокой части выпуклости наносить ни в коем случае нельзя, иначе она неравномерно поднимется над общей поверхностью заготовки. Периодически заготовку отжигают (отжиг снимет внутреннее напряжение металла, возникающее под воздействием ударов, так называемый наклеп или нагартовку, и возвращает металлу пластичность), наносят круглогубцами гофры и осаживают их на стойне.
Когда необходимая глубина достигнута, выколотку прекращают, поверхность заготовки выглаживают гладильником, излишки материала на краях обрезают и зачищают заусенцы напильниками, наждачной бумагой и т. д.
Мастера старины были настоящими виртуозами выколоточных работ. Здесь и уже известные нам выколоточные молотки и опорные стойна, и «желобильни» – чугунные плиты с углублениями для выгиба краев дна у чайников, ведер, других изделий, и «осадки» с «обжимками» – толстые металлические стержни длиной 200–250 мм с углублениями на концах, применявшиеся для изготовления заклепок. Здесь и гладильники – подобия кузнечных гладилок применяли мастера и различные молотки: наводильники для осадки гофр, шаровые – для сферических поверхностей, шеечные – для образования шеек ваз, кубков, кувшинов.
Рис. 3.9. Выколотка полусферы на стойче ручным способом:
А – загиб края заготовки; б – гофрирование края; в – посадка гофров; г – выколотка середины; д – нанесение гофров; е – посадка гофров.
Кроме простых изделий мастера изготовляли сложные сборные конструкции. Здесь и самовары, и упомянутые уже кувшины, кубки, вазы. Элементы этих произведений (шейки, тулова, ножки) изготовлялись по отдельности, а затем соединялись при помощи фальцев. Такие детали как ручки, краны самоваров и др. отливались по формам и щедро украшались подчас уникальным узором. В настоящее время сборку отдельных элементов можно производить пайкой или сваркой.
Облегчало труд умельцев применение болванок. Болванки старых мастеров представляли собой чугунные опоры, имевшие форму и размеры готового изделия или его детали. Технику выколотки на болванках применяют и в настоящее время. Она ускоряет и упрощает процесс изготовления изделия и его деталей и даже может лечь в основу серийного производства изделий.
Болванки можно изготавливать из дерева, металла, стеклопластика, текстолита и даже камня. Рабочая поверхность болванки должна быть очень ровной и отполированной. Заготовку прикладывают к болванке и начинают выколачивать, передвигаясь от краев к выпуклости. Периодически заготовку снимают с болванки и подвергают отжигу. Вернув металлу пластичность, продолжают придавать заготовке форму болванки. Завершив формовку, изделие проглаживают, срезают излишки материала, зачищают заусенцы.
Сборку многоэлементного изделия производят пайкой. Чтобы соединительный шов не выделялся, его проковывают в холодном или нагретом состоянии молотками или небольшой по весу кувалдой. При термической (горячей) правке осуществляют местный нагрев заготовки в деформированной части. Делать это можно над газовой горелкой. Прогревают заготовки постепенно. За один проход вдоль деформированной части нагревают зону шириной в 0,5–2 толщины материала заготовки. Выравнивание происходит при охлаждении прогретой зоны в силу сжатия металла при переходе из горячего состояния в холодное. Дополнительная проковка шва позволяет увеличить эффект термической правки.



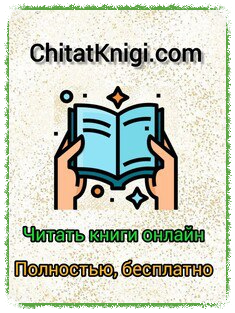
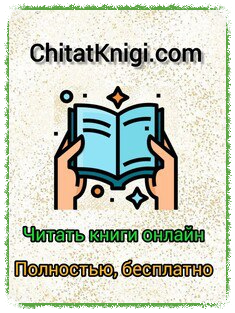
